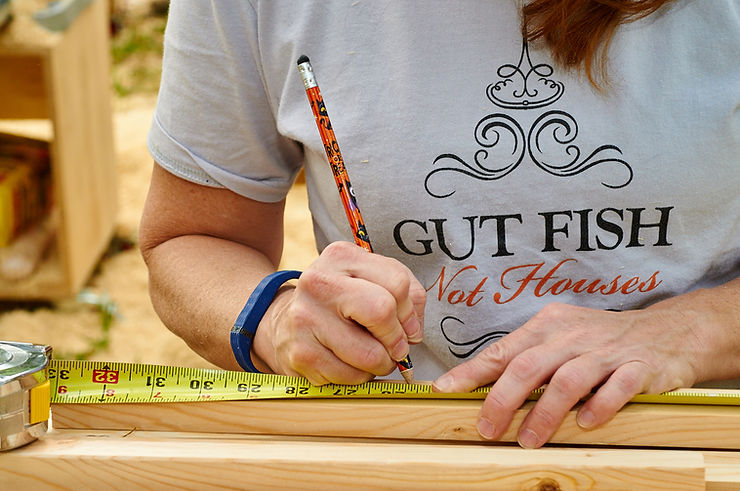
A measuring tape was one of the first tools I learned how to use, though I don’t directly remember the specifics of learning how to use one. Who knows. Maybe it was the ruler in elementary school. I took drafting in the seventh grade and we used rulers in that class. Took shop class, so theoretically there was one there. By the time I dropped out of school to crawl under houses and go full time into construction, I had somehow learned how to find measurements on a tape and distinguish between halves, quarters, eighths and sixteenths in relation to whole numbers.
Keith King and David Buchanan, the master carpenters I cut my teeth with, helping them do the work on high end homes in the old part of San Antonio, taught me phrases like, “half inch light,” or “a strong nine sixteenths.” Curtis Miller, the framing contractor who taught me how to build the structure of a home, used this method as well. “Cut the next one ninety six and a sixteenth strong.” Now, when I am making a window sash for a typical Tampa historic home, I like my finished thickness to be one and three eighths, on the light side. I know the exact spot where my machines need to be set to achieve that too.
There’s more to using a measuring tape than is blatantly obvious. I’ve learned, and have seen with my own eyes, that different brands of measuring tape will give you different versions of twelve inches. Even measuring tapes of the same brand can give false readings. I’ve had a carpenter take the tape out of my hand, compare the reading with their own tape, and discover that I’d dropped it and bent the hook in a way that threw everything off. He became suspicious when every cut came back wrong. When he found out, he showed me how to bend the hook back to where it was supposed to be. Told me to get a new tape, because the one I dropped wouldn’t ever be the same and couldn’t be trusted.
I’ve learned, and have seen with my own eyes, that different brands of measuring tape will give you different versions of twelve inches. Even measuring tapes of the same brand can give false readings.
That was back before measuring tapes had cheater fractions on them. I’ve tried every brand of tape worth trying, Stanley silver twenty five footers, thirty footers, thirty-five footers, green sixteen footers, the big Fat Max, a little keychain Fat Max three footer, and all the Leverlocks. I tried a Lufkin brand once that had a retraction spring so strong and violent that when it pulled the tape ribbon back into the box, it sliced my finger wide open. I’ve had Craftsman brand, tapes from Harbor Freight, DeWalt tapes, Walmart, Home Depot, Lowe’s brand and probably a lot of others I’ve forgotten, but my favorite? That’s just a regular Stanley, twenty five foot. It used to be the silver twenty five footer.

But now it’s the green Stanley twenty five footer. Or at least it used to be a green Stanley. Something happened at Lowe’s Home Improvement. The exact Stanley that I used to buy for eight dollars, now says Craftsman on the label and the tape ribbon is no longer the Stanley traditional yellow. It’s white. But it’s the same one. There’s no bells and whistles. Just an honest, retractable tape measure that’s not overpriced. I have been using measuring tapes long enough to have a valid opinion. And that’s what you are about to get.
The measuring tapes I hate are those with the fractions printed right on the tape ribbon. My suggestion? Learn the measuring tape that doesn’t have the cheater fractions on it. Yeah. Cheater fractions. Having those on a measuring tape is kinda like never learning how to multiply and carrying a cheat sheet around with you everywhere you go. Now they even have tapes that divide the number you are looking at in two.
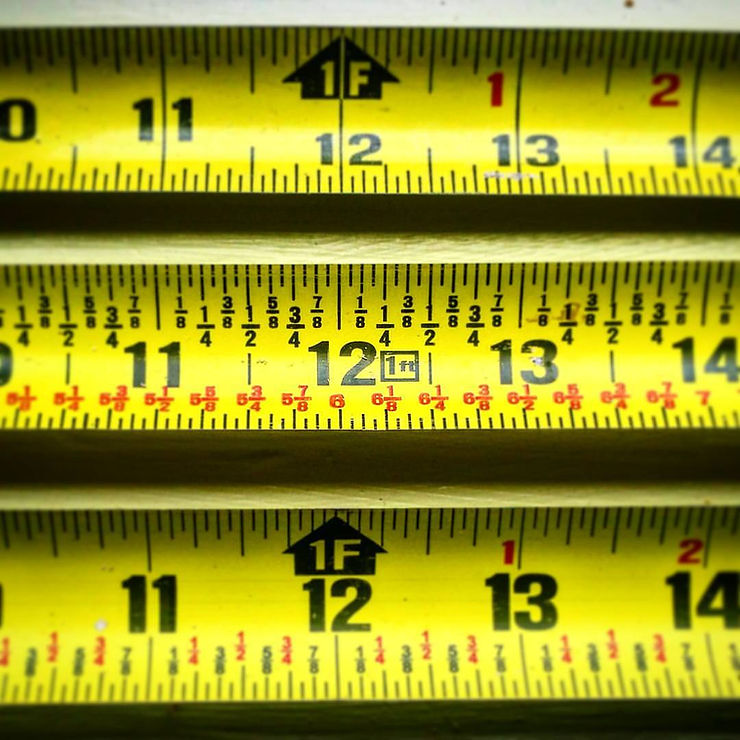
Measuring is more than knowing where the five eighths mark is. It’s more about knowing, or recognizing the spacial relationship between the lines. Where is the half? The quarter inch? The three quarters? A person must become adept at recognizing the proper spacing between the lines, irrelevant of any numerical indicators, because as one eventually learns, the numerical indicators, and even the hash marks, are all relative and subjective anyway. A strong quarter inch. Seventeen and a sixteenth light. The marks are relative to where the actual cut takes place. When you mark fourteen and seven eighths, is it a big seven eighths or a small one? And where in relationship to the hashmark on your tape, is your cut? For that matter, where is the mark on your piece to be cut, in relation to the mark on your tape? And then, where do you cut, relative to that? The printed fractions, the numerical indicators, disappear in light of these questions and serve only as an unnecessary addition, a safety net, Dumbo’s feather in relation to the reality that the measuring tape attempts to teach the artisan.
Therefore, proper measuring has nothing to do with the actual numerical indicators, whether feet and inches, or meters, centimeters and millimeters. Proper measuring has everything to do with your mark, how you find where to place it, where you place it, and where you cut in relation to the mark you made.
Tape measure manufacturers might say that adding the cheater fractions, those numerical indicators to the tape ribbon is merely an innovation driven by consumer demand. Actually the opposite is true.
Can we all agree that there is practically zero attempt, with reference to big corporate interest, to build an army of artisans, of problem solvers? Are there instructions with each purchase that teach the nuances of using such a basic device? Is there a movement to teach this fundamental and important basic skill? No. Rather there is an all too easy acceptance of trade ignorance that serves as low hanging profitable fruit. Is consumer demand actually for a tape with fractions? Or is this an easy way to subtly assist with keeping a status quo, or even a status quo that is undergoing a long, drawn out and downward spiral? Do the corporations merely stand idly by and watch as the artisan population dissolves into thin air? Of course they do. When that happens, they will have just the product, ready to fill this market void, this absence of the meddling little people.
Where is the actual demand? Is it not for an actual person? An artisan who can help solve the problems you encounter? When you call the corporation with your important problems to solve, is it with the robot machine that you’d rather speak? Or do you press zero repeatedly until you get a person, who hopefully will empathize with your plight and help you solve the problem? Given the opportunity, you go to the real person. You want a person who knows the measuring tape, for real. Or do you really think the people prefer the planned obsolescence being offered in place of actual, long term solutions? Do you think people as a whole actually prefer buying things they know will break? Do you prefer someone in another country reading cookie cutter solutions to you off of a computer screen?
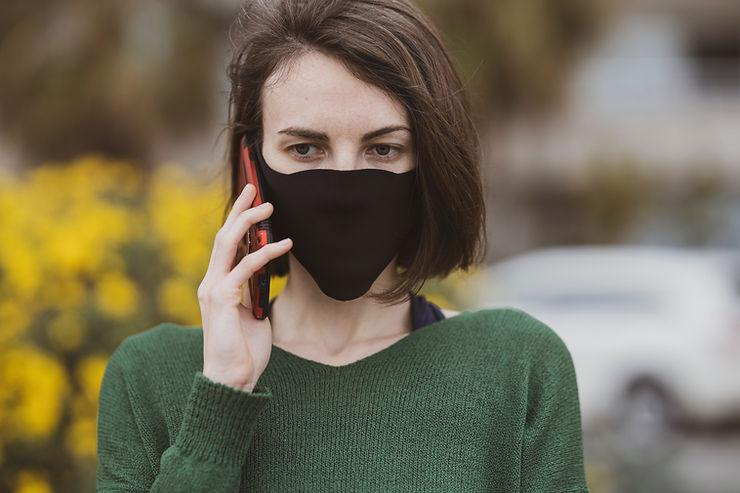
Am I just imagining the chute the cattle are herded into? Are they not being told, against their better judgment, against their own intuitions, that “This is the way?” Not only that “This is the way,” but that, “This is the ONLY way.” Are there really no other solutions other than what we’re being shown? You are telling me that measuring tapes with fractions are now the new, and only way? This is the way of the masses? This is the best that can be done? Will we require no more of the people we hire than a measuring tape with fractions printed on it? This is really who you want at your house solving your problems? Someone who can’t even read a measuring tape?
This is the best that can be done? Will we require no more of the people we hire than a measuring tape with fractions printed on it? This is really who you want at your house solving your problems? Someone who can’t even read a measuring tape?
Sorry. No. This is not the Artisan Way. I cannot accept this. I cannot accept that this is who we were designed to be. And I know that you are with me. Tell me you don’t prefer competence and ability over ignorance and impotence. You can’t. Because given the opportunity, you seek what is to you, an obvious solution to your problem. Someone should be able to help you. Not being able to find one, you accept what is offered and made easily available. Tell me this isn’t true. You accept with a dull reluctance, a temporary solution designed to fail, that when it does, you go out and purchase another temporary solution designed to fail – over and over and over and over.
Artisans do not deal in failure, but rather what can be an arduous, but rewarding and fulfilling upward spiral of vision, possibility and growth. Artisans don’t trick the masses into buying into failure. Artisans don’t deal in obsolescence, but rather innovation that optimizes both materials and work into an archetypal reality that is timeless.
How does one innovate a measuring tape? By putting fractions on it? With a laser? True innovation is hard, and innovating past the simple tape as we know it might be a long way off, at least as far as humans are concerned. Printed fractions aren’t an innovation, they are Dumbo’s feather communicating that it’s ok for the trades to be dumbed down. While we wait for an actual innovation to optimize the tape’s functionality, it is better to consider innovating and optimizing ourselves, mastering the movements required to understand the spacial relationship between the hash marks, to understand where to put your mark in relationship to the marks on your tape, and then where to make the cut in relation to where you made your mark. This is the Artisan Way
Master a movement.
Master a sequence of movements.
Master sequencing your sequences.
Master with intention.
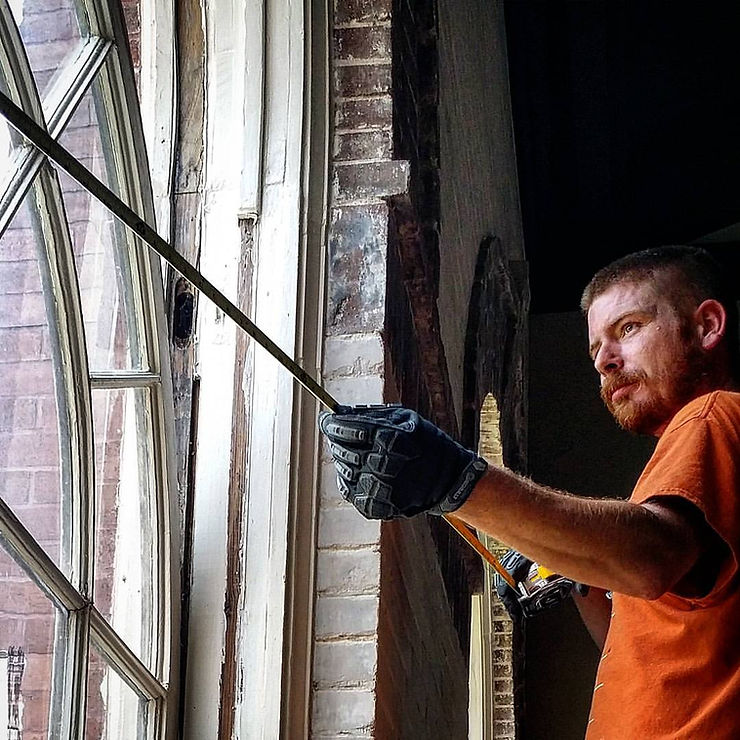